Inverter Motors and Their Revolutionary Role in Dryers
In today’s fast-paced world, energy efficiency and technological advancements play a pivotal role in shaping our everyday lives. One such innovation that has been quietly revolutionizing household appliances, including dryers, is the inverter motor. In this article, we delve into the intricate workings of inverter motors and explore how they are making their mark in the world of drying appliances, as being an important part of dryers in many terms.
What is a Inverter Motor?
An inverter motor is a type of electric motor that utilizes cutting-edge electronics to control its speed and torque. Unlike traditional motors, which operate at a fixed speed, inverter motors offer variable speed control. This is achieved by converting the incoming AC power into DC power and then utilizing advanced semiconductor devices to convert it back into a controlled AC power output. This variable frequency and voltage control allow the motor to adapt its speed and power consumption to the requirements of the task at hand.
Whom invented the inverter motor?
The invention and development of the inverter motor technology have been a collaborative effort involving contributions from various researchers, engineers, and companies over several decades. It’s important to note that the concept of variable-speed motors and the use of power electronics for motor control evolved gradually over time. As such, there isn’t a single individual credited with inventing the inverter motor in the same way that a single inventor might be associated with a specific invention.
However, the groundwork for inverter motor technology was laid through advancements in power electronics and motor control theory. Engineers and researchers in the fields of electrical engineering and power electronics played key roles in developing the technologies that eventually led to the creation of inverter motor systems.
In the 1960s and 1970s, advancements in semiconductor technology, such as the development of insulated gate bipolar transistors (IGBTs) and metal-oxide-semiconductor field-effect transistors (MOSFETs), provided the necessary components for building efficient and reliable inverter circuits. These advancements enabled the precise control of AC power frequency and voltage, which are essential for inverter motor operation.
Various companies and institutions worldwide contributed to the development and commercialization of inverter motor technology. Companies specializing in electric drives, automation, and power electronics were instrumental in bringing inverter motor systems to market. As demand for energy-efficient and variable-speed solutions increased, inverter motor technology found applications in a wide range of industries, including manufacturing, HVAC systems, transportation, and household appliances.
In conclusion, the invention and development of inverter motor technology can be attributed to the collective efforts of engineers, researchers, and companies across multiple disciplines. This collaborative progress over time led to the creation of the advanced motor control systems we know today as inverter motors.
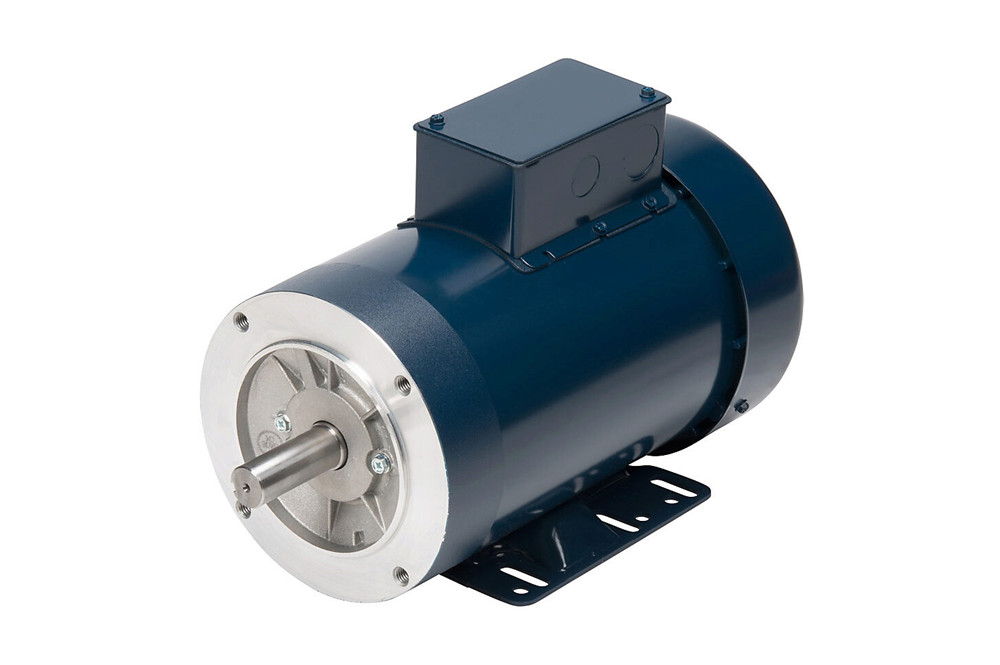
How The Inverter Motor Works?
An inverter motor operates using advanced electronics to control its speed and performance. The working principle of an inverter motor involves converting the incoming electrical power to a form that can be precisely adjusted, allowing the motor to adapt its speed based on the requirements of the task. Here’s a step-by-step explanation of how an inverter motor works:
- AC to DC Conversion: The process begins by converting the standard AC (alternating current) power from the electrical grid into DC (direct current) power. This is achieved using a rectifier circuit, which typically consists of diodes that allow current to flow in one direction only, effectively converting the AC waveform into a smoother DC waveform.
- DC to AC Conversion: Once the power is in DC form, it’s then converted back into AC using an inverter circuit. The inverter consists of advanced semiconductor devices like insulated gate bipolar transistors (IGBTs) or MOSFETs. These devices can switch on and off rapidly, creating an AC waveform with varying frequency and voltage.
- Variable Frequency Control: The key feature of inverter motors is their ability to control the frequency of the AC power supplied to the motor. By changing the frequency of the AC waveform, the motor’s rotational speed can be adjusted. Higher frequencies result in faster speeds, while lower frequencies result in slower speeds.
- Precise Speed Control: The inverter continuously monitors the load and operational requirements of the motor. Based on this input, it adjusts the frequency of the AC power to achieve the desired speed. This dynamic control ensures that the motor operates at the most efficient speed for the task, minimizing energy consumption.
- Torque Control: Inverter motors also offer control over torque. Torque refers to the twisting force that causes rotation. By adjusting the voltage supplied to the motor, the inverter can control the torque output, which is particularly useful when dealing with varying loads or when a sudden burst of power is required.
- Feedback Mechanism: Many inverter motors incorporate feedback systems such as encoders or sensors. These devices provide real-time information about the motor’s speed and performance to the inverter. This data enables the inverter to make accurate adjustments, ensuring precise and consistent operation.
- Dynamic Adaptation: Inverter motors excel in applications where the load changes frequently. For instance, in household appliances like washing machines or dryers, the motor can adjust its speed and torque according to the weight of the load or the moisture level of the clothes.
- Energy Efficiency: The ability to adjust speed and torque based on demand significantly enhances energy efficiency. Traditional motors often run at full power regardless of the task, leading to energy wastage. In contrast, inverter motors consume only the energy required to achieve the desired outcome.
In summary, the inverter motor’s operation revolves around converting and controlling electrical power in a way that enables precise speed and torque adjustments. This dynamic adaptability leads to improved energy efficiency, better performance, and quieter operation in a wide range of applications.
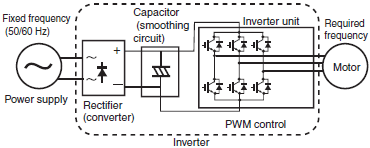
What are the components of inverter motor?
Inverter motors are complex systems that incorporate various components to enable their variable-speed and efficient operation. The specific components can vary depending on the application and the design of the motor, but here are the key components commonly found in inverter motor systems:
Power Supply
Inverter motors require a power supply that provides electrical energy to the system. This power supply can be connected to the electrical grid or another power source.
Rectifier Circuit
The rectifier circuit is responsible for converting the incoming AC power from the grid into DC power. This is achieved using diodes that allow current to flow in one direction only, resulting in a smoother DC waveform.
DC Link Capacitor
The DC link capacitor is used to store energy in the form of DC voltage. It helps to stabilize the DC voltage and supply a smooth source of power to the inverter circuit.
Inverter Circuit
The heart of the inverter motor system is the inverter circuit. This circuit consists of advanced semiconductor devices such as IGBTs (insulated gate bipolar transistors) or MOSFETs (metal-oxide-semiconductor field-effect transistors). The inverter circuit converts the DC power from the DC link capacitor back into controlled AC power with adjustable frequency and voltage.
Microcontroller/Processor
Inverter motor systems are often controlled by microcontrollers or processors. These components receive input from various sensors and control signals, and they execute the algorithms needed to adjust the motor’s speed and torque.
Sensor System
Sensors play a crucial role in inverter motor systems. They provide feedback on parameters such as motor speed, temperature, load conditions, and more. This real-time data is used by the control system to make adjustments and ensure optimal performance.
Voltage Source Inverter (VSI)
The voltage source inverter is a key component of the inverter circuit. It generates the AC output voltage by rapidly switching the DC voltage from the DC link capacitor using the IGBTs or MOSFETs.
Control Algorithms
Inverter motor systems utilize complex control algorithms to regulate the frequency and voltage of the AC output. These algorithms ensure that the motor operates at the desired speed and torque for the given task.
Cooling and Heat Dissipation Components
Inverter motors generate heat due to the switching of power electronics components. Cooling mechanisms such as fans, heat sinks, and cooling fins are employed to dissipate heat and maintain proper operating temperatures.
Output Stage
The output stage of the inverter motor system connects to the motor itself. It provides the controlled AC power to the motor’s windings, enabling the motor to rotate at the desired speed and generate the necessary torque.
Motor
The motor is the primary component that converts electrical energy into mechanical motion. In inverter motor systems, the motor is designed to accommodate variable-speed operation, making it more efficient and adaptable to different tasks.
These components work in harmony to enable the variable-speed and energy-efficient operation characteristic of inverter motor systems. The integration of advanced electronics, sensors, and control algorithms distinguishes inverter motors from traditional fixed-speed motors, allowing for greater precision and optimization in various applications.
What is the difference between Inverter Motor and Other Types?
Inverter motors stand in stark contrast to conventional motors, which operate at a constant speed regardless of the load or demand. Traditional motors often lead to energy wastage due to their inability to adjust their speed based on real-time needs. In contrast, inverter motors shine in terms of energy efficiency by optimizing their speed to match the workload, thus minimizing energy consumption.
What are the Advantages of Inverter Motors?
- Energy Efficiency: Inverter motors are significantly more energy-efficient than traditional motors. By adjusting their speed according to the task, they consume only the required energy, leading to reduced electricity bills and a smaller carbon footprint.
- Variable Speed Control: The ability to control the speed of the motor offers numerous benefits, such as fine-tuning drying cycles in dryers. This prevents over-drying, leading to improved fabric care and prolonged garment life.
- Reduced Noise and Vibration: Inverter motors operate with less noise and vibration compared to conventional motors, contributing to a quieter and more pleasant user experience.
Where inverter motors are used?
Inverter motors find applications across a wide range of industries and sectors due to their energy-efficient, variable-speed capabilities. These motors have become increasingly popular as advancements in technology have made them more reliable and cost-effective. Here are some common areas where inverter motors are used:
- Household Appliances:
- Inverter motors are commonly used in household appliances such as washing machines, dryers, refrigerators, air conditioners, and vacuum cleaners. They enable these appliances to adjust their operation to match the load and desired settings, resulting in energy savings and improved performance.
- Industrial Applications:
- In industries, inverter motors are employed in various applications such as conveyor systems, pumps, fans, compressors, and blowers. Their ability to vary speed and torque according to demand makes them ideal for processes where loads can change dynamically.
- HVAC Systems:
- Heating, ventilation, and air conditioning (HVAC) systems benefit from inverter motors’ precise control of airflow and cooling capacity. Inverter-driven HVAC systems can adjust their output based on room temperature and occupancy, optimizing energy consumption and comfort.
- Transportation:
- Inverter motors are used in electric and hybrid vehicles, trains, trams, and even ships. These motors offer efficient power delivery, regenerative braking capabilities, and adaptability to varying operating conditions.
- Commercial Buildings:
- Inverter motors are integrated into systems like elevators, escalators, and automated doors. Their flexibility in adjusting speed and torque ensures smooth and energy-efficient operation in these high-traffic areas.
- Renewable Energy:
- Inverter motors play a crucial role in renewable energy systems such as wind turbines and solar tracking systems. They convert the variable energy output from these sources into stable AC power for distribution.
- Factory Automation:
- In manufacturing processes, inverter motors are used in robotics, conveyors, material handling, and precision machining systems. Their ability to respond to real-time changes in production needs enhances efficiency and reduces downtime.
- Medical Equipment:
- Inverter motors are used in medical devices such as MRI machines, X-ray equipment, and laboratory instruments. Their precise control and quiet operation are essential in maintaining a stable environment for patient care and diagnostics.
- Agricultural Machinery:
- Farming equipment like irrigation systems, grain conveyors, and poultry feeders benefit from inverter motor technology. The ability to adapt to changing conditions ensures optimal use of resources.
- Commercial Kitchens:
- In the food industry, inverter motors are used in commercial kitchen appliances such as ovens, grills, and mixers. These motors help maintain consistent cooking temperatures and controlled mixing speeds.
- Water Treatment and Pumping Stations:
- Inverter motors are employed in water treatment facilities and pumping stations to regulate water flow and pressure according to demand, optimizing energy usage.
In summary, inverter motors are found in a diverse array of applications where energy efficiency, precise control, and adaptability to varying conditions are crucial. Their ability to reduce energy consumption, enhance performance, and prolong equipment life makes them a valuable technology across multiple industries.
Inverter Motors in Dryers: A Perfect Match for Efficiency
Evolution of Dryer Appliances
Dryers, once characterized by their energy-intensive operation, have undergone a transformative journey towards energy efficiency. Inverter motors have played a key role in this transformation by redefining how dryers operate.
What is the Role of Inverter Motor Role in Dryers?
The heart of a dryer lies in its motor, responsible for spinning the drum and driving the airflow that dries the clothes. Inverter motors have redefined this role by offering variable speed control, enabling dryers to adjust the drum rotation speed and airflow intensity according to the fabric type, load size, and moisture level.
What are the Benefits Inverter Motor Role in Dryers?
- Energy Savings: Inverter motor-equipped dryers use energy only as needed, minimizing wastage during operation. This translates to substantial energy savings over time.
- Enhanced Drying Performance: With variable speed control, inverter motor dryers ensure even drying across different fabric types. Delicates receive gentle treatment while bulkier items are efficiently dried.
- Improved Fabric Care: Over-drying can lead to fabric wear and tear. Inverter motors prevent this by enabling precise control over drying times and temperatures, resulting in longer-lasting clothes.
What are the Features of Dryer’s Inverter Motor ?
Variable Speed Control for Drying Cycles
Inverter motor dryers employ sophisticated algorithms to adjust the drum rotation speed throughout the drying cycle. This ensures that the clothes are evenly exposed to heat and airflow, promoting efficient drying while preventing excessive heat damage.
Smart Sensors for Precision
Modern inverter motor dryers come equipped with advanced sensors that detect both the load size and moisture level. These sensors communicate with the motor’s control system, allowing for real-time adjustments to optimize drying performance and energy usage.
User-Friendly Interfaces and Connectivity
Inverter motor dryers often feature intuitive control interfaces that allow users to customize drying settings based on preferences and fabric types. Additionally, many models offer connectivity options, enabling remote monitoring and control through smartphone apps, contributing to a more seamless laundry experience.
Navigating Challenges and Looking Ahead
Initial Investment and Long-Term Gains
While inverter motor-equipped dryers may carry a higher initial cost, the long-term benefits in terms of energy savings and fabric preservation often outweigh the upfront expense.
Maintenance Considerations
Maintenance and repair of inverter motor dryers require specialized knowledge due to the advanced electronics involved. However, advancements in design and technology are making these appliances more reliable and user-friendly over time.
Consumer Education
As inverter motor technology gains momentum, educating consumers about the benefits and proper usage of these appliances becomes crucial. Proper understanding ensures optimal utilization and maximum energy savings.
What is the Inverter Drive Technology?
Inverter drive technology, also known as variable frequency drive (VFD) technology, is a sophisticated system used to control the speed and torque of electric motors. This technology offers precise control over motor operation by adjusting the frequency and voltage of the electrical power supplied to the motor. The primary goal of inverter drive technology is to enhance energy efficiency, optimize performance, and extend the lifespan of motor-driven systems. Let’s explore the intricacies of inverter drive technology:
How the Inverter Drive Technology Works?
Inverter drive technology revolves around manipulating the frequency and voltage of the electrical input to an AC (alternating current) motor. The basic principle involves converting the incoming AC power into DC (direct current) power through a rectifier circuit. The DC power is then converted back to AC with adjustable frequency and voltage using an inverter circuit that contains advanced semiconductor components like IGBTs (insulated gate bipolar transistors) or MOSFETs (metal-oxide-semiconductor field-effect transistors).
By varying the frequency of the AC power, the speed of the motor can be adjusted. Higher frequencies result in faster motor speeds, while lower frequencies lead to slower speeds. Simultaneously, adjusting the voltage controls the torque output of the motor, allowing for precise control over the mechanical power delivered by the motor.
What is the difference of Inverter motors and Inverter drive technology?
Inverter drive technology involves controlling motor speed and torque through adjustable frequency and voltage, optimizing energy efficiency and control in industries like manufacturing and HVAC. Inverter motors, designed for this technology, operate at adjustable speeds, offering energy efficiency and precise control, finding use in various applications such as appliances, industrial equipment, and transportation.
What are the Benefits of Inverter Drive Technology?
- Energy Efficiency: Inverter drive technology enables motors to operate at optimal speeds based on the actual load and demand. Traditional motors run at a fixed speed, often resulting in energy wastage during periods of low demand. In contrast, inverter-driven motors consume only the necessary energy, leading to significant energy savings.
- Soft Start and Stop: Inverter drives facilitate smooth start and stop of motor operation. This eliminates the abrupt mechanical stress that comes with direct-on-line starting, reducing wear and tear on equipment and enhancing equipment lifespan.
- Precise Control: In applications requiring accurate speed and torque control, such as conveyor systems or HVAC units, inverter drive technology ensures consistent and precise performance. This adaptability to varying loads improves process efficiency and product quality.
- Reduced Mechanical Stress: The gradual acceleration and deceleration provided by inverter drives minimize mechanical stress on equipment, reducing maintenance costs and downtime.
- Regenerative Braking: In some cases, inverter drives can convert the kinetic energy generated during braking back into electrical energy, which can be fed back into the power supply system. This regenerative braking feature further enhances energy efficiency.
- Flexible Operation: Inverter drives allow for remote monitoring and adjustments. This remote accessibility enhances convenience, facilitates troubleshooting, and aids in optimizing system performance.
What are the Applications of Inverter Drive Technology?
Inverter drive technology finds applications across numerous industries and sectors, including:
- Manufacturing and Industrial Processes: Conveyor systems, pumps, fans, compressors, and CNC machines benefit from the precise control and energy efficiency of inverter drives.
- HVAC Systems: Heating, ventilation, and air conditioning systems optimize energy consumption and provide more accurate temperature control using inverter drive technology.
- Renewable Energy: Inverter drives are integral to solar power systems and wind turbines, converting variable energy sources into stable AC power for the grid.
- Transportation: Electric vehicles and trains employ inverter drives to control motor speed and regenerative braking.
- Household Appliances: Washing machines, refrigerators, and air conditioners use inverter drives to enhance efficiency and adapt to varying loads.
Future Trends and Beyond
Integration with Smart Homes
The integration of inverter motor dryers into smart home systems is on the horizon. This will enable seamless coordination between appliances, energy management systems, and user preferences for a more intelligent and efficient home.
Advancements in Efficiency and Sustainability
Ongoing research and development are focused on enhancing the efficiency of inverter motors, further reducing energy consumption and environmental impact. These efforts align with the global shift towards sustainability.
FAQ Inverter motor
What is an inverter motor?
An inverter motor is an electric motor that utilizes advanced electronics to control its speed and performance. Unlike conventional motors that operate at fixed speeds, inverter motors can vary their speed based on the task’s requirements. This variability is achieved by adjusting the frequency and voltage of the electrical power supplied to the motor, enabling energy-efficient and adaptable operation.
What is the difference between an inverter motor and a normal motor?
The primary difference between an inverter motor and a normal motor lies in their speed control capabilities. Inverter motors offer variable speed control by adjusting the frequency and voltage of the power supplied, allowing them to adapt to changing load conditions. In contrast, normal motors operate at a fixed speed, regardless of the load. Inverter motors are more energy-efficient, reduce wear and tear, and provide precise control, while normal motors have a single fixed speed and tend to consume more energy.
Can an inverter run an electric motor?
Yes, an inverter can run an electric motor using the technology known as a variable frequency drive (VFD). The inverter controls the speed of the electric motor by adjusting the frequency and voltage of the power supplied to it. This is particularly useful for applications that require variable speeds, energy efficiency, and precise control. Inverter-driven motors are commonly used in household appliances, industrial machinery, transportation systems, and various other sectors where adaptable motor performance is essential.
How does an inverter washer dryer work?
An inverter washer dryer operates using advanced electronics to control the motor’s speed and performance. Instead of fixed-speed operation, the motor’s speed is adjusted based on the load and fabric type. This variability ensures energy efficiency and optimal drying. The inverter technology enables smooth and gradual adjustments, preventing abrupt starts and stops, resulting in gentler fabric care and reduced wear on the machine.
What is a heat pump inverter dryer?
A heat pump inverter dryer is an advanced drying appliance that combines heat pump technology with inverter motor control. Heat pumps extract heat from the air and use it to dry clothes, making them highly energy-efficient. When combined with an inverter motor, the dryer’s performance becomes even more adaptable, using variable-speed motor control to adjust drying cycles based on load size and moisture levels, resulting in precise and energy-efficient drying.
How much power does a dryer motor have?
The power of a dryer motor can vary based on the type and capacity of the dryer. Standard household dryer motors typically range from 1/4 to 1/2 horsepower (HP), equivalent to around 186 to 373 watts. Inverter motor-equipped dryers can adjust their power consumption based on load requirements, enhancing energy efficiency by using only the necessary power for optimal drying.
Where does a dryer draw air from?
Dryers draw air from the surrounding environment, typically through a vent located on the front or back of the machine. This air is heated and circulated through the drum, absorbing moisture from the clothes. The air is then vented outside, carrying away the moisture and leaving the clothes dry. Proper venting is essential for efficient drying and preventing the buildup of humidity in the laundry area.
Conclusion
As inverter motor technology continues to advance, its influence on household appliances like dryers is undeniable. The benefits of energy efficiency, fabric care, and adaptable performance make inverter motor dryers a staple in modern homes. With ongoing innovations and a growing awareness of sustainable living, the era of inverter motor appliances is set to shape a greener and more efficient future.